Fractured Chains: Successive crises and supply chain resilience
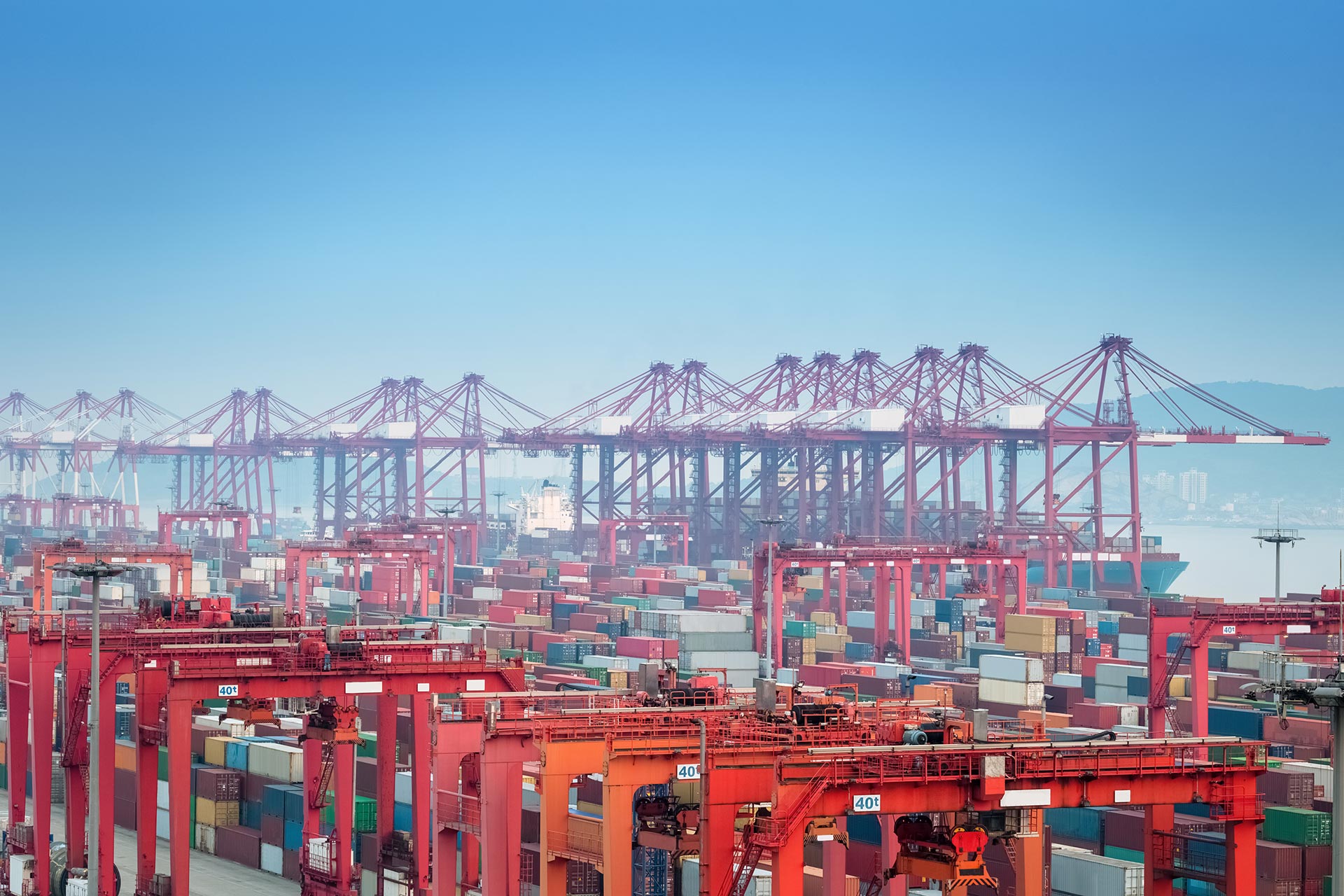
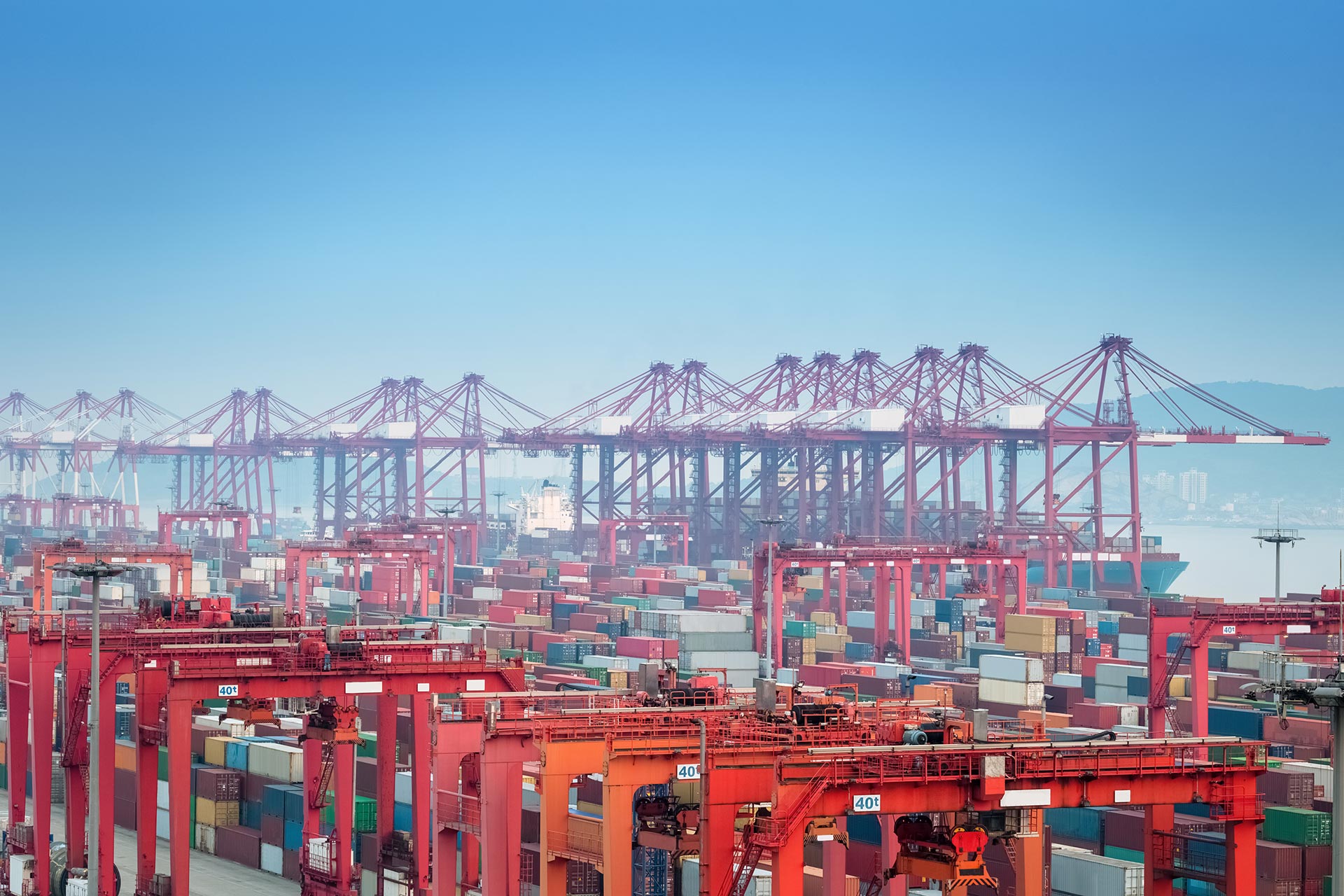
Supply chain resilience refers to an organisation’s ability to quickly and efficiently alter its suppliers in the event of a disruptive scenario. This can be done in many ways, including via contingency planning, diversification, and selection of robust and proximal suppliers. Most organisations can also bolster the effectiveness of these measures by incorporating contingency planning and threat monitoring into their decision making.
As of 2022, supply chain resilience is at the forefront of business leaders minds. The successive crises we discussed in our opening Fractured Chains post have had far ranging, and often difficult to immediately quantify effects on the third, fourth and fifth parties that many firms rely upon for parts, services and personnel. Here, we’ll take a look at a couple of case studies that demonstrate where supply chain shocks can occur, and how organisations can prepare for and shield themselves against them.
Case Study 1 - Shanghai Lockdowns
A series of snap lockdowns across China’s major manufacturing hubs are continuing to contribute to overall price inflation, particularly in the West. Overland travel between commercial hubs is severely restricted, and staffing at ports is limited, with both problems contributing to a slowed intake of cargo and containers at strategic ports.
This has lead to the secondary effects of shipping congestion in Chinese waters, as well as lengthened journey times. Longer journeys also mean more containers are out at sea as opposed to being loaded/unloaded across the global port network, driving a shipping container shortage, and increasing shipping costs.
- Since the beginning of the year, at least 27 Chinese cities have been under full or partial lockdown, impacting up to 185 million residents across the country.
- As of April 2022, ships from China to Seattle were taking four days longer than expected to arrive.
- Nearly 20% of container vessels globally were waiting outside congested ports, according to analysis published by Windward as of late April 2022.
- At the peak of the lockdown in Shanghai, containers were sitting for as many as 15 days at the port before being picked up by truckers, up from fewer than 5 days when the restrictions first took effect.
- In April 2022, the global freight rate index stood at about $7,800, up from $5,000 in 2021 and $1,500 in 2020.
While China is heavily relied upon for much of the world’s manufacturing, the ruling CCP often make snap decisions (such as no-notice lockdowns) that contribute to an unstable commercial environment for foreign businesses. Facing into these challenges, both the American and European Union chambers of commerce said in May that their members are rethinking their supply chains and whether to expand investment in the face of China’s zero tolerance approach to combating COVID-19. Unfortunately this indicates that many businesses have been caught ‘flat footed’, unable to exit their current supply chains for alternates in time to prevent major impacts to their operations and bottom line.
Case Study 2 – Semiconductor Shortages
Semiconductors are the essential component of microchips for everything from cars and computers, to microwaves. Semiconductor shortages have been felt globally since late 2020, mainly due to the COVID-19 pandemic. Not only did factory shutdowns and social distancing measures lead to delays in production at already busy factories, but the subsequent huge shift towards home working has increased demand for technology such as laptops, tablets and webcams. This in turn has driven up demand for cloud computing and internet services.
COVID-19 is not the only issue however. Interestingly, the value of semiconductors has historically been quite volatile due to rapidly changing supply and demand; meaning makers don’t want to over-invest in multi-billion-pound factories for fear demand will disappear and profits could collapse. That means the industry is now playing catch-up to meet sustained demand for chips in everything from smartphones to cars, and businesses are beginning to realise how important understanding the long-term viability of their suppliers is.
Alongside pandemic measures and patchy historic investment, geopolitics will likely play a significant role in the future availability of semiconductors, given the locations that their component raw materials are produced:
Silicon
At present, China is the world’s largest producer of silicon, one of the key components of semiconductors, with a production volume estimated at six million metric tons in 2021 – more than double the rest of the world combined. The second largest producer of this metalloid in the world is Russia, which produced 580,000 metric tons in the same year. As sanctions on Russian entities and trade tariffs on Chinese exports continue to bite, the price of this commodity, and the chips that are reliant on it, will continue to climb. Additionally, the availability of the resource itself may become a bargaining chip (pardon the pun) in future discussions between China and the West.
Neon
Russia’s war in Ukraine has also had a dramatic effect on the availability of neon, also critical to the production of semiconductors. Two Ukrainian companies, Cryoin and Ingas, who between them provide 45-55% of the world’s semiconductor-grade neon, were forced to close their factories in Odessa and Mariupol due to the Russian invasion. Even if the conflict were to abate, both companies were heavily reliant on purchasing by-products of Russian steel manufacturing in order to produce neon in vast quantities; a situation that is unlikely to be repeated even in the event of peace or a sustained ceasefire.
Whilst many companies have excellent supply chain assurance programs in place, fewer are looking deeper at fourth and fifth-parties, or attempting to understand where they are vulnerable to the next shock to the global system. It is imperative that companies with long or complex supply chains begin to analyse their vulnerabilities, identify appropriate risk indicators and integrate these with contingency plans that can be activated in order to minimise the impact of critical shortages.
Building supply chain resilience
Understanding and managing supply chain exposures is difficult, and requires a proactive approach in order for organisations to respond effectively. Below we have outlined four areas businesses should look to improve their supply chain resilience.
Impact & risk assessment
During this stage, the organisation should leverage any existing tools it has, such as business impact analyses or continuity plans, to fully understand its most important service lines or processes, and identify the suppliers that support them. This will help define the level of impact likely to be sustained in the event that they cannot operate. Organisations should then conduct scenario planning to understand and quantify the risks that these suppliers face, and inform contingency plans.
Contingency planning
Once the most at-risk suppliers have been identified, mitigations should be considered to reduce the organisations exposure to this risk. Such measures should be mutually reinforcing where possible and may include the diversification of suppliers, strengthening contractual exit arrangements, stockpiling, on-shoring of outsourced services or exiting current suppliers if needed. Any contingency plans should be exercised robustly with all stakeholders to ensure their viability.
Ongoing monitoring
Once contingencies are in place, it is important organisations know when to activate them through monitoring of identified key risk indicators (KRIs), via multiple intelligence streams. This may include social media/online monitoring for specified indicators and warnings, or deeper ongoing analysis in critical areas of operations. As little as 24 hours notice in high-risk scenarios may be the difference between an organised pivot away from a problem area or substantial losses.
Response
Key risk indicators allow organisations to ‘ramp up’ their response to developing supply chain issues in a considered manner, ensuring internal stakeholders are briefed appropriately before a risk becomes a crisis. This allows designated leaders to respond much quicker in the event of a significant problem and deploy mitigation measures or contingency plans as necessary to reduce the impact of supply chain shocks.
What's inside?
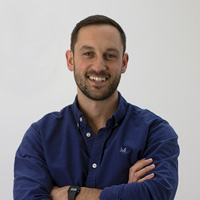
Stay a step ahead in an increasingly complex and unpredictable world
Our consultants stay on top of the latest megatrends that influence how organisations are attacked, whether related to terrorism, criminality, war or cyber.
We document their analysis here. Be the first to see it.